The SeatBridge system is not just an innovation; it’s a revolution in how cars are assembled and experienced. Designed to replace traditional seat installation methods, SeatBridge introduces a sleek and efficient approach that benefits manufacturers, seatmakers, and passengers alike.
Why SeatBridge Matters
• Enhanced Efficiency: Simplifies assembly with a one-shot mounting process for front seats, central console, and wiring.
• Improved Passenger Experience: Increases rear passenger legroom by 170mm and transforms interiors from a “workshop” look to a “sitting room” aesthetic.
• Cost and Weight Optimization: Removes 7 body brackets, simplifying car body structures and improving overall strength.
The Prototype Phase
ABACAD is collaborating with SBSIntec to initiate the development of a groundbreaking SeatBridge prototype.
This prototype will demonstrate how SeatBridge integrates seamlessly into existing car designs, offering manufacturers a glimpse of its potential to enhance production workflows and elevate the driving experience.
The complete Development Document is available at the bottom of this post.
Hereafter are the highlights of this document:
1. Streamlined Assembly Process
The SeatBridge enables a fully pre-assembled Front Seats Assembly (FSA), including seats, central console, and wiring, to be mounted in a single step on the production line.
2. Structural Improvements for Car Bodies
By eliminating seven seat brackets, the SeatBridge simplifies car body designs while enhancing overall strength and reducing complexity.
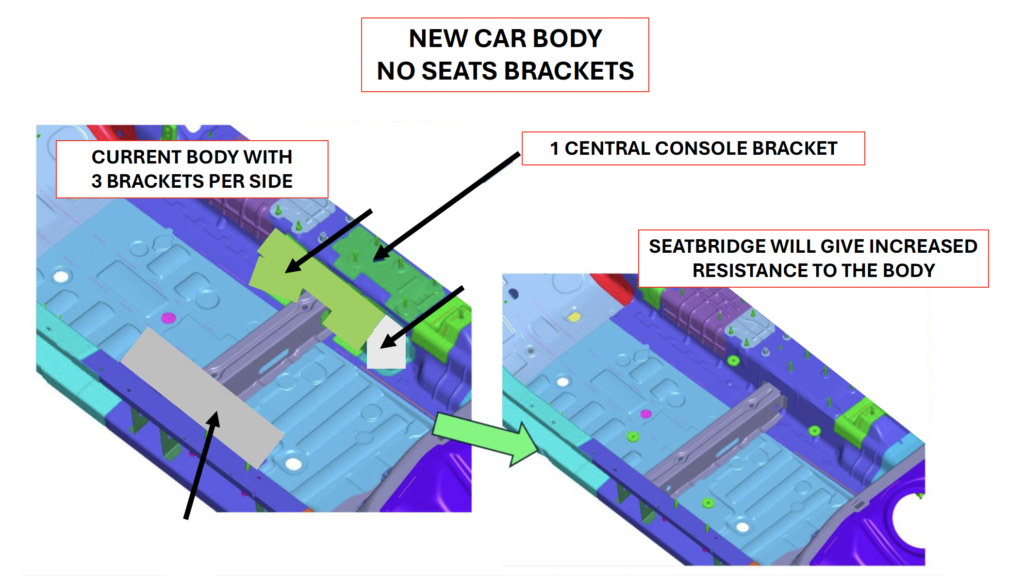
3. Passenger Comfort Upgrades
Rear foot space increases by 170mm, offering unparalleled comfort. With no protruding spikes and a single, easy-to-clean carpet per side, the passenger experience transforms into a luxurious “sitting room” feel.
4. Universal Compatibility
SeatBridge can integrate seamlessly with sliding tracks used by seatmakers today, requiring only minor adjustments to track lengths and configurations.